Duct System for Cowboys Stadium in Arlington, TX
The evening of June 6, 2009, was a typical Texas summer night with the temperature still a hot, humid 89°F. However, inside the new Cowboys Stadium in Arlington, Texas, concert attendees for the first-ever event in the new venue were cool and comfortable in the massive arena, thanks in part to spiral ductwork fabricated by Spiral Pipe of Texas Inc.
Fans that came to hear country music stars George Strait and Reba McEntire may have been partially distracted by the spectacle of the brand-new, $1 billion stadium that had been the focus of so much attention in the north Texas and national media since the project was first announced by its developer, Dallas Cowboys owner Jerry Jones.
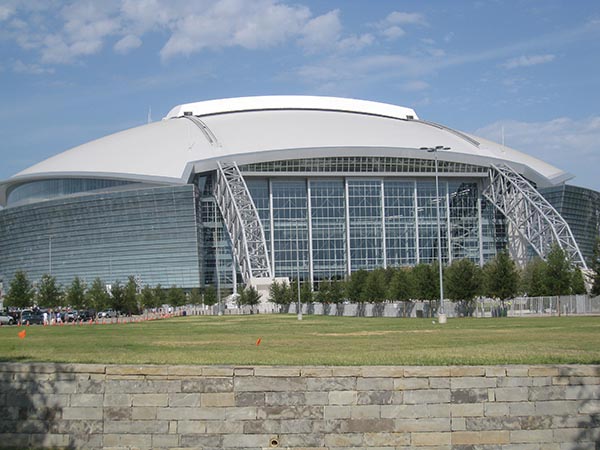
New Dallas Stadium Was A ‘Spot-On’ Project
Spiral Pipe, which also uses the acronym “SPOT,” has successfully completed high-profile projects in the past but none in the company’s 28-year history compared to this, officials said. The construction project from beginning to end has been chronicled in many media outlets, including an episode of cable TV’s “Build it Bigger” series on the Science Channel.
“This project was special. It is safe to say that every person in our company was excited to be associated with part of the construction of this world-class venue,” said Frank Schlekewy, SPOT’s plant superintendent. “Our people were proud of meeting the challenges the project presented and being able to report to family and friends that they were a part of building the new home of the Dallas Cowboys.”
Preferred
SPOT has long been a preferred fabricator for contractors that are looking to partner with a company able to meet the challenges of high-profile, large-scale projects. SPOT customer TD Industries of Dallas entrusted the entire “bowl duct” component of the project while fabricating much of the stadium’s other duct in its own sheet metal shop.
Spiral Pipe officials said they were grateful for the opportunity to work with TD Industries, a company widely regarded as the go-to contractor for state-of-the-art sports arenas, having recently worked on the Arizona Cardinals stadium near Phoenix.
TD awarded the project to SPOT in February 2007. Considering the need to condition air inside an 80,000-plus seat stadium while its retractable roof is closed, the spiral duct specified was huge. Much of the duct was 92 inches in diameter and 8 feet long.
SPOT has long been a preferred fabricator for contractors that are looking to partner with a company able to meet the challenges of high-profile, large-scale projects.
The challenge was not in the complex design of the duct system as much as it was in material handling, officials said. Fabricating, installing angle ring flanges, lining, and maneuvering each massive piece through the shop during production and ultimately on to a flatbed trailer proved to be difficult. Innovations such as rolling duct cradles, designed and fabricated by SPOT, allowed for each piece to be rolled from spiral machine, to welding station, to lining station, to protective wrapping station, and then to storage by a single person. Angle-ring hangers were bolted to completed pieces to allow each piece to be staged and loaded by forklift without damaging the completed product. Special brackets were designed and built to be attached to the 92-inch elbows, allowing the duct to be securely strapped during transit. The same brackets were also used to crane lift the large elbows into their staging area at the jobsite. Those few innovations saved countless man-hours and were credited by Spiral Pipe workers in maintaining a safe environment throughout the project.
Coordination
Although the stadium was less than 17 miles from SPOT’s facility, shipping coordination was key as the company worked with Cecil Wilkins Trucking to handle over 220 scheduled flatbed deliveries up Interstate 30 to the stadium jobsite.
The project design called for spiral duct because of its superior energy efficiency, lower installation costs, and the long-term benefits when compared with square duct systems.
All duct was internally lined with Johns Manville’s Spiracoustic Plus duct liner provided by SPOT vendor Pamaco. The Manville liner allowed each joint of duct to be significantly lighter than traditional dual-wall duct, making the pieces easier to manipulate into position by the installing contractor. Galvanized angle rings supplied by Midwest Metal Products were factory installed on each piece of duct.
The first shipments consisting of mechanical room duct were made toward the end of August 2007.
The project was segmented into eight packages. SPOT fabricated and stored the completed duct and fittings at its plant in Fort Worth, Texas, until the jobsite was ready for shipment. Each piece was wrapped to protect from weather and construction debris, color-coded by area, and individually numbered for inventory and installation instruction. These numbers coordinated with SPOT’s computer-aided drafting assembly drawings and helped the installing contractor ensure that each piece was installed in proper order.
Spiral pipe was essential for a large-scale job requiring high energy efficiency, multiple long-term benefits, and low installation cost.
‘A Mirror Image’
Packages of the project were fabricated, delivered and installed in an order that allowed the first half of the project to be a mirror image of the second half. After SPOT had completed the first half, the company then gained the confidence of knowing they had seen and built each piece before.
By the time the last release shipped out in January 2009, the shipping and delivery of stadium duct became a near “nonevent” because all involved in the supply chain had become so familiar with the procedures.
“Completing a project like this does boost our confidence as we approach other jobs that require large-diameter duct — ‘extreme duct,’ ” project superintendent Schlekewy said. “Since the Cowboys Stadium project, we have built 84-inch diameter duct for a project in New Mexico and 96-inch duct for a church in Louisiana. Our fabrication crew approached those jobs as if they were routine.”
As with any team effort, good communication was a key to this project’s success, officials added.
Spiral Pipe’s vice president of sales, Steve Dockery, followed this job from quote to completion, taking on the additional responsibility as project manager. Dockery dealt directly with TD Industries field superintendent Bert Newton.
“Working with TD, and especially Bert, was a pleasure for all of us at SPOT,” said Dockery. “I can honestly say that all were amazed that this project progressed so easily. That is a testament to planning upfront and the skill and professionalism of all involved.
“I know that all of us at SPOT and Bert’s crew at TD are proud every time we see the duct, whether on TV or in person.”
Spiral Pipe workers were very efficient, Newton recalled. “The accuracy of SPOT’s duct saved my crew from having to make adjustments in the field,” he said. “On-time delivery helped us meet the demands of our installation schedule. I would definitely recommend working with SPOT. I hope to work with them again on future spiral duct jobs.”
Browse OurDuct Solutions
Spiral Pipe of Texas (SPOT) fabricates high quality, MADE IN THE USA sheet metal products for the heating, air conditioning and ventilation (HVAC) industries.